Premium Perspex® Clear Cast Acrylic Sheet
From £{{ (incVAT() ? initialPrice.incVAT : initialPrice.exVAT).toFixed(2) }} £{{ (incVAT() ? initialPrice.salePriceIncVAT : initialPrice.salePriceExVAT).toFixed(2) }} {{ incVAT() ? incVATTranslation : exVATTranslation }} £{{ (incVAT() ? initialPrice.incVAT : initialPrice.exVAT).toFixed(2) }} {{ incVAT() ? incVATTranslation : exVATTranslation }}
Listed below is a range of multipacks, rainbow packs (one of every available colour) and clearance items all of which are available at significantly discounted prices.
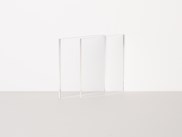
5mm - Pack of 20 (250mm x 250mm) - *** 40% DISCOUNT ***
- Thickness: 5mm
- Width: 250mm
- Height: 250mm
- Edge finish: None
- Pack size: 20
Was £107.04 Was £89.20 Now £64.22 Now £53.52
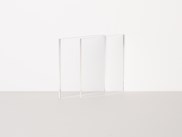
6mm - Pack of 20 (250mm x 250mm) - *** 40% DISCOUNT ***
- Thickness: 6mm
- Width: 250mm
- Height: 250mm
- Edge finish: None
- Pack size: 20
Was £123.84 Was £103.20 Now £74.30 Now £61.92
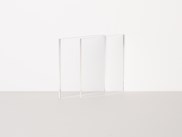
Pack of 25 x 3mm A4
- Thickness: 3mm
- Width: 210mm
- Height: 297mm
- Edge finish: None
- Pack size: 25
Was £88.20 Was £73.50 Now £72.77 Now £60.64
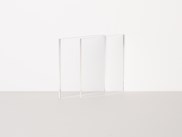
Pack of 25 x 3mm A3
- Thickness: 3mm
- Width: 420mm
- Height: 297mm
- Edge finish: None
- Pack size: 25
Was £170.40 Was £142.00 Now £140.58 Now £117.15
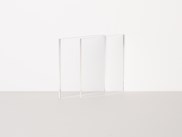
Pack of 25 x 5mm A4
- Thickness: 5mm
- Width: 210mm
- Height: 297mm
- Edge finish: None
- Pack size: 25
Was £133.50 Was £111.25 Now £110.14 Now £91.78
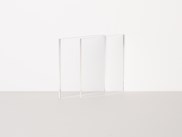
Pack of 10 x 15mm A1
- Thickness: 15mm
- Width: 594mm
- Height: 841mm
- Edge finish: None
- Pack size: 10
25% off the equivalent of 10 x A1 panels!
Was £1,063.56 Was £886.30 Now £691.31 Now £576.09
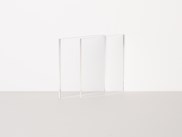
Pack of 25 x 15mm A1
- Thickness: 15mm
- Width: 594mm
- Height: 841mm
- Edge finish: None
- Pack size: 25
A huge 40% saving versus the equivalent of 25 x A1 panels!
Was £2,658.90 Was £2,215.75 Now £1,130.03 Now £941.69
Bespoke Fabrication
We have the machinery and expertise to manufacture bespoke items in acrylic, polycarbonate and many other plastics, from one-offs to large production runs. Read more about the various services we offer, or complete the form below to request a quote.
CNC Routing
Our advanced Multicam Apex 3R (3 Axis) CNC routers allow us to provide an extensive range of precision CNC routing services. Read more
CNC Laser Cutting
Laser cutting is a fabrication process that uses a thin, intensely focused stream of light to cut through a range of different materials, including plastics and acrylics. Read more
Diamond & Flame polishing
Edge polishing is a fabrication process that polishes the edges of acrylic panels, removes any cutting marks, and achieves a smooth, glossy finish. Read more
Rotary & Laser Engraving
Laser engraving is a fabrication process that uses a laser beam to physically remove the surface of a material to create an indentation that is noticeable to both the eye and touch. Read more
Line Bending
Line bending is a process that’s used to make precise folds in plastic and acrylic components. Our line bending fabrication service allows us to bend plastic and acrylic sheets along a defined ‘line’ – without any need for gluing or joining. Read more
Have bespoke requirements?
Complete this form and we will get back to you with a quote.
Clear cast acrylic, also commonly referred to as Perspex Sheet, is a high quality and versatile clear plastic sheet material offering high levels of strength and clarity. Suitable for many applications, cast acrylic sheet is an easy material to work with.
Key features
- Excellent optical clarity
- High gloss finish
- Hard wearing
- Weather resistant
- Easy to work with/fabricate
- Lightweight
Typical applications
- Glazing
- Signage
- Furniture
- Model fabrication and display
- Retail display
- Point of sale
- Point of purchase
Detailed description
Optical clarity
Clear cast acrylic has an exceptionally high level of light transmission allowing 92% of all visible light through the material creating an unparalleled crystal clear finish. Not even glass can achieve this level of optical clarity. Because of this clear cast acrylic is an excellent alternative to glass for glazing purposes.
Hard wearing
Cast acrylic is one of the hardest thermoplastic sheet materials available and its attractive aesthetics remain for longer than other plastic sheet materials.
Light weight
While offering higher levels of clarity than glass, clear cast acrylic weighs half as much as an equivalent glass panel making fabrication, installation and transportation a far more attractive proposition.
High gloss finish and easy to clean
Its high gloss finish is not only very attractive but also more practically very easy to clean.
Weather resistant
With excellent resistance to the elements, cast acrylic performs well outside. No significant changes in appearance are expected over 10 years.
Manufacturing process
Cast acrylic is manufactured by pouring monomer between two sheets of high quality glass and polymerised in batches in a carefully controlled manufacturing process.
Recyclable
Cast acrylic can be recycled all the way back to its original raw material, the monomer.
Cut to Size Perspex
Our cut to size service enables you to purchase Perspex panels at the dimensions you require without having to purchase the manufactured sheet size, normally 3m x 2m. We do not charge for cutting standard shapes/sizes that are available on our website, however we do also offer additional options such as drilled holes, rounded corners and edge polishing. In addition to our cut to size service, we also offer more bespoke fabrication services including:
Brands
Perspex®, PlexiGlass®
Country of Manufacture
UK
Stock sheet sizes
3050mm x 2030mm, 2440mm x 1220, 2030mm x 1520mm
Minimum panel size
50mm x 50mm
Maximum panel size
3050mm x 2030mm
(1mm thickness = 1220mm x 1220mm)
Light transmission
92%
Relative density
1.19 g/cm³
Manufacturers thickness tolerance
+/- 10 % plus 0.4mm (e.g. 5mm cast sheet could vary from 4.1mm to 5.9mm)
Cutting tolerance
+/- 1mm
Material protection
Protective film on both sides
Fire rating
UK Class 3 Fire Rating
Service temperature
-40 to 80°c
Vicat softening temperature
>110°c
Water absorption
0.2%
Material Name/Scientific Name
Poly(methyl methacrylate) "PMMA"
Manufacturers guarantee
10 Year against discolouration
Recyclable
Yes
Recycled content
Maximum 3%
Data sheets
We provide a fast delivery service throughout the UK using recognised Couriers such as Royal Mail, DHL, and Parcel Force.
Delivery prices are calculated based on the length of the longest side of the material ordered i.e. the delivery price of a panel measuring 1500mm x 1000mm would be based on the 1500mm dimension. Only one delivery charge is charged per order regardless of how many items are ordered.
UK Delivery costs
Longest side | Standard Delivery | Express Delivery | Order value for FREE delivery |
---|---|---|---|
Samples (100mm x 100mm) | £2.95 | £9.95 | £250 |
Less than 500mm | £6.95 | £12.95 | £250 |
500mm to 999mm | £9.95 | £19.95 | £250 |
1000mm to 1999mm | £14.95 | £24.95 | £250 |
2000mm or greater | £19.95 | £29.95 | £250 |
Standard delivery for all accessories is £7.95, or £12.95 for Express delivery.
All prices listed include VAT.
Delivery Times
Our guidelines for delivery times are listed below:
- Standard delivery (3-5 working days)
- Express delivery (2-3 working days)
Express Delivery
If you require faster delivery you may wish to consider choosing our Express Delivery option at the checkout. Express Delivery orders are prioritised over standard orders and delivered using a recognised nationwide courier.
Next Day Delivery
Next Day delivery is not available via our website due to the volume and bespoke nature of orders we receive on a daily basis. However, if you need to place an order and require Next Day delivery please contact us – we will make every effort to meet your requirements and deadlines.
European/EU Delivery
We have temporarily disabled European delivery for orders placed through our website whilst we make changes to ensure that the correct rate of EU VAT is being charged. Our team can however manually process orders so please contact us if you require delivery to the European Union.
Remote Areas
Due to the nature of the ”made to measure” products we supply, we provide delivery prices at a standard rate and reserve the right to cancel an order should it become economically unviable to fulfill the order. In these extremely rare circumstances, the customer will be contacted first to discuss alternative options.
When delivering to some locations we can incur increased Courier delivery costs. Should delivery be required to one of the locations listed below a remote area supplement will be automatically added to the price of delivery during the checkout process.
Longest side | Remote area supplement |
---|---|
Samples (100mm x 100mm) | £0.00 |
Less than 500mm | £0.00 |
500mm to 1499mm | £10.00 |
1500mm to 2499mm | £15.00 |
2500mm or greater | £20.00 |
All prices listed include VAT.
Examples of delivery locations which may incur a remote area supplement are:
- Channel Islands
- Isle of Man
- Isles of Scilly
- Isle of Wight
- Scottish Islands
- Scottish Highlands
- Remote areas of Scotland
- Northern Ireland
If you require delivery to one of these areas please get in touch to discuss your order.
Third-Party Deliveries
Some products are dispatched directly from the manufacturer and delivered by a third-party courier. If applicable, this is clearly stated on each Product page under the 'Delivery' tab/section.
Can I collect my order from Simply Plastics?
Yes, of course. Orders can be collected from our premises in Colchester, Essex. At the final stage of the checkout process there is a delivery option labelled "Collection/pickup" which is free. Once your order is complete, you will be notified by email along with our address and collection times.
I need my order urgently, can I pay for faster shipping?
Yes. We offer an express delivery service which aims to deliver all orders in 1-3 working days. Orders are delivered by a recognised courier company and may require a signature on delivery.
Do you have a minimum order charge or small order fee?
This is a question we are asked fairly regularly due to the previlance of either a minimum order charge or small order fee within the industry.
At Simply Plastics our approach has always been to treat all orders equally, small or large. We want all customers, new and existing, to be able to place orders with us confident that they are only paying for the products and materials that they require. We therefore do not have a minimum order charge or small order fee.
What are polished edges?
When we cut an acrylic sheet to size, the saw blade/router toolbit produces a matte finish on the edges of the panel. We use a technique called diamond polishing to polish the edges to a bright, smooth and glossy finish.
Our diamond edge-polishing machine polishes the edge of acrylic by running a rotating, diamond tipped wheel along the edge of the material.
You can read more about the techniques used to polish Perspex® in our blog post, The Ultimate Guide to Polishing Perspex®.
What are the uses of Perspex
Perspex is used in a vast variety of different ways - it's chemical properties, wide range of colours and finishes, availability and cost, make it the material of choice in applications and industries ranging from home repairs and general DIY through to construction, furniture design, retail displays, signage, lighting and interior design. In the home it can be used to replace broken greenhouse glass panels, as bathroom/kitchen splashbacks or even to replace broken picture frame glass. In commercial environments acrylic mirrors, acrylic block for retail displays and LED diffusers for lighting are commonly used. We stock and supply all of the Perspex product ranges, all of which we can provide cut to size and ready for use.
Is it possible to cut acrylic sheet myself?
Acrylic sheet can be cut using a circular saw, a jigsaw or any type of saw with a fine tooth blade. We recommend laying the acrylic flat on a firm surface, such as a workbench, and clamping it down before cutting. If you are using clamps to hold the material down, we suggest placing wood between the clamps and acrylic sheet to prevent any damage to the surface of the acrylic. Manufacturer safety precautions should always be followed when using any type of saw. Please read our "how to cut acrylic sheets" blog post for more detailed information.
Can I buy Perspex(R) acrylic sheets near me?
Depending on where you live within the UK, it may be possible to buy acrylic sheets locally, however you should be aware that most of the large DIY retailers will only stock clear acrylic, in a small selection of sizes and thicknesses, which means you'll need the tools to cut it to size at home. The advantage of buying from Simply Plastics is that you can purchase the exact size you require, there will be no wastage and you don't need any tools to cut to size - furthermore, to make it easier we'll deliver it directly to your home or workplace just a few days later. We are based in Colchester, just 30 minutes from London but we deliver right across the UK.
Why is Clear Extruded acrylic cheaper than Clear Cast acrylic?
Cast acrylic is generally regarded as a better quality material and offers a number of advantages over the extruded variant such as having a higher optical clarity and superior surface finish, being more resistant to chemicals and solvents, less prone to scratching, easier to machine and fabricate and available in a far wider range of colours and surface finishes i.e. gloss/matte. The manufacturing process for cast acrylic is longer and more complex than that of extruded acrylic which in-turn generally makes extruded acrylic slightly cheaper.
What is the difference between cast acrylic and extruded acrylic?
Acrylic is manufactured in two versions - cast and extruded. Cast acrylic is made by pouring the hot liquid acrylic ingredients between two sheets of glass which are separated by rubber gaskets - the thickness of the gasket determines the thickness of the acrylic sheet being made. The sealed glass plates are placed into an oven and allowed to heat during which the chemical processes and changes take place. Finally, the sheets are allowed to cool. Cast acrylic is commonly used for glazing, signage and retail displays. Extruded acrylic is made by pouring hot liquid acrylic ingredients into a form or die before the acrylic is forced through rollers which leaves the material with an even thickness and finish. Cast acrylic is generally regarded as a better quality material and offers a number of advantages over the extruded variant such as being more resistant to chemicals and solvents, less prone to scratching, easier to machine and fabricate and available in a far wider range of colours and surface finishes i.e. gloss/matte. Extruded acrylic is commonly used for lighting applications, interior decoration and screening.
Whats the difference between Plexiglass and Plexiglas®?
These two terms are pronounced the same and spelt almost identically, however, Plexiglass is the genericized trademark or proprietary emponym that has become synonymous with acrylic sheeting in most of Europe and North America whereas Plexiglas® is the brand name for acrylic sheets manufactured by Röhm GmbH in Germany. Whilst Plexiglass has become the generic trademark for acrylic sheets in Europe and North America, the brand name Perspex® is synonymous with acrylic sheeting in the UK.
Whats the difference between Plexiglas® and Perspex®?
Both Plexiglas® (most commonly spelt Plexiglass) and Perspex® are brand names of Acrylic sheet. Röhm GmbH, based in Germany, are the manufacturers of Plexiglas® whereas Perspex® is manufactured in the UK by Perspex International Limited. Both manufacturers supply a wide range of colours and thicknesses. Whilst the brand names Plexiglas® and Perspex® are different, ultimately the acrylic sheet that they manufacture is the same albeit each manufacturer might tweek the formulation to increase or enhance UV-resistance, light transmission or colour.
Which applications are best suited to Cast or Extruded Acrylic?
When deciding whether Cast Acrylic or Extruded Acrylic is best for your project it’s worth considering the specific application and desired finish you hope to achieve. The table below provides some examples of the most suitable type of acrylic sheet to use for specific applications.
Cast Acrylic | Extruded Acrylic | |
Application |
|
|
In our experience, whilst some projects/applications will require specific characteristics of either Cast or Extruded Acrylic, in most cases the choice can be made based on either colour, thickness or cost, as below:
- Clear or Colour: Extruded acrylic is generally only manufactured in clear, black and white and therefore if there is a requirement for any other colour, Cast Acrylic is the only choice.
- Thickness: Cast acrylic is commonly manufactured in thicknesses up to 100mm whereas extruded is generally available in a maximum thickness of 20mm (Simply Plastics stock up to 50mm in Cast and 10mm in Extruded).
- Cost: Extruded is marginally cheaper and therefore any requirement for a large quantity of sheets/panels, where the benefits of cast acrylic are not important, is likely to be more cost effective produced in Extruded acrylic.
How can I calculate the weight of a Perspex Panel?
All of the different types of plastics that are available on our website, whether they be a panel, a disc, tube or rod, show the weight of the piece you require once you have entered your dimensions, shown in grams or kg.
The weight of any plastic can be calculated using the simple formula: Weight = Volume x Density
Read our blog post on how to calculate the weight of a variety of different plastics covering panels, discs, road and tube.